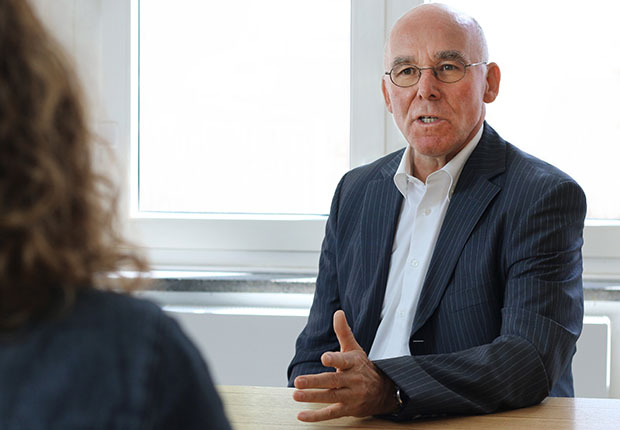
Lean Ergonomics-Experte Ulrich Fröleke erklärt, was sich hinter dem Begriff Lean Ergonomics verbirgt und wie sich Produktionsprozesse damit auf intelligente und wirtschaftliche Art und Weise reorganisieren lassen.
WIR: Herr Fröleke, Sie gelten in der Branche als ein ausgesprochener Experte für Lean Production und Ergonomie und befassen sich bei Treston Deutschland mit dem Thema. Warum sind diese beiden Begriffe, die ja u. a. über das Toyota Production System weltweit bereits in den 1980er Jahren bekannt wurden, heute immer noch topaktuell?
Fröleke: Herstellungsprozesse haben sich während der letzten zwei Jahrzehnte massiv verändert und beschleunigt. D.h. der Druck auf Produktion, Mitarbeiter und Unternehmen wächst. „Just-in- time“ oder etwa „On-demand“ sind populäre Konzepte, die in vielen Branchen auf ganz unterschiedliche Art und Weise umgesetzt wurden. Die Begriffe sind gewissermaßen eine Fortsetzung des Lean-Gedankens. Sie implizieren theoretisch das Vorhandensein von schlanken Produktionsprozessen, aber sie implizieren nicht das Vorhandensein von ergonomischen Arbeitswelten. In vielen Fällen führt diese Beschleunigung zu einer Überlastung der menschlichen Arbeitskraft. Die Frage lautet also, wie kann ich das vermeiden?
WIR: Lassen Sie mich raten … durch Lean Ergonomics?
Fröleke: Richtig. Die Aufgabe ist, intelligenter zur arbeiten, Arbeit zu reorganisieren. Menschen müssen entlastet werden, damit sie ihre Arbeit so lange und so konstant wie möglich ausüben können. Dabei bedingen diese beiden Konzepte einander. Das hat schon das Toyota Production System gezeigt. Bis heute ist diese Verbindung zwischen Lean-Prinzipien und Ergonomie und den Möglichkeiten, die sich daraus ergeben, vielen kleinen und mittelständischen Unternehmen, die halbautomatisierte Herstellungsprozesse fahren – in denen also Menschen arbeiten -, nicht klar, obwohl sie vielleicht schon über schlanke Produktionsstrukturen verfügen und sogar ergonomisch Arbeitswelten entworfen haben, von denen das eine allerdings nicht zum anderen passt.
WIR: Es kommt also auf die Sichtweise an, wie Lean Production und Ergonomie sich einerseits konzeptionell ergänzen und wie das dann praktisch in der Produktion umgesetzt wird?
Fröleke: Ja. Denn nur wer konzeptionell von dieser Verbindung überzeugt ist, wer bereit dazu ist, wird erkennen, dass eine Integration von Lean und Ergonomie zu Lean Ergononmics enorme Potentiale für Unternehmen bietet, die sich positiv auf die Produktivität, die Wettbewerbsfähigkeit und die Mitarbeiter auswirken.
WIR: Wenn Sie von Überzeugung sprechen, meinen Sie den Unternehmer?
Fröleke: Ja. Es liegt an ihm, zu erkennen und zu entscheiden. Und zwar aus einem ganz einfache Grund: Komparative Wettbewerbsvorteile gelten nicht ein Leben lang, sie sind ständig vom Wandel bedroht. Wer einzig und allein ans Ergebnis denkt, der wird langfristig scheitern, es sei denn, er ist bereit, auf diesen Wandel aktiv zu reagieren ihn zu gestalten. Zum Beispiel durch Prozessorganisation und Prozessoptimierung mit Lean Ergonomics. Wir vertreten allerdings die Auffassung, dass die Geschäftsführung Lean Ergonomics nicht ohne den Mitarbeiter umsetzten sollte, denn er ist es schließlich, der unter diesen Bedingungen arbeiten muss. Auch wenn Ergonomie per se gut gemeint ist, kann dieser Schuss nach hinten losgehen, wenn der Mitarbeiter außen vor bleibt.
WIR: Was ist jetzt neu an dieser nicht mehr so neuen Sichtweise?
Fröleke: Mal ganz praktisch gesprochen: Es geht um die Organisation von Produktionsprozessen. Lean Ergonomics liegt der Ansatz zu Grunde, dass sich Ergonomie und Lean perfekt ergänzen. Aus gutem Grund: Weil Ergonomie den Menschen in seiner Arbeitswelt entlastet, kann dieser besser, entspannter und kontinuierlicher arbeiten. Erstrecht unter den Bedingungen einer schlanken Produktion, die natürlich darauf abzielt, Herstellungsprozesse zu optimieren und zu beschleunigen, Gewinne zu maximieren, Kosten zu minimieren, und die Produktivität konstant zu steigern. Dieses Ziel erreichen Unternehmen aber nur, wenn eine effiziente Allokation aller erforderlichen Ressourcen stattfindet und Verschwendung vermieden wird. Dazu zählen u. a. auch Fehlzeiten der Mitarbeiter, die überwiegend auf Grund von muskuloskelettalen Erkrankungen auftreten, wie verschiedene Jahresberichte von Arbeitsschutzorganisationen zeigen. Ein Grund: Produktionsprozesse sind zwar schlank, aber nicht ergonomisch organisiert. Mitarbeiter sind durch einseitige und sich ständig wiederholende Bewegungsabläufe überlastet und ermüden, weil sie nicht durch entsprechende Hilfen unterstützt werden. In der Summe führt das zu Produktionsausfällen. Solche Entwicklungen sind nicht unbekannt. Für jene Wertschöpfungsprozesse, die auf menschliche Arbeitskraft angewiesen sind, ist das natürlich fatal.
WIR: Welche Gegenmaßnahmen können Unternehmen hier konkret ergreifen?
Fröleke: Der Unternehmer sollte seinen Produktionsprozess genau analysieren, sowohl unter Lean- Gesichtspunkten als auch unter ergonomischen Gesichtspunkten. Denn eine Produktion kann zwar schlank sein, aber nicht unbedingt ergonomisch, wenn Mitarbeiter sich bei Ihrer Arbeit durch Bewegungsabläufe, die nicht ihrer Physiologie entsprechen, regelrecht kaputt arbeiten. Ein Grundsatz von Lean Ergonomics ist: work smarter, not harder. Es geht also darum zu prüfen, wie etwa der Produktionsprozess organisiert und aufgebaut ist, wie die erforderlichen Materialien oder Halbfertigerzeugnisse diesem Produktionsprozess zugeführt werden und welche Hilfsmittel den Mitarbeiter in diesem Prozess unterstützen. D. h. gleichzeitig finden sowohl der schlanke Prozess als auch die Arbeit auf einer ergonomischen Grundlage statt, wonach der Mitarbeiter den Arbeitsplatz im Idealfall an seine Bedürfnisse ergonomisch zu hundert Prozent anpassen kann. Wir haben auf der Basis von diesem Denkansatz zahlreiche Unternehmen aus der Elektroindustrie, der Logistik und der Verpackungsindustrie beraten und Lean Ergonomics-Projekte auf verschiedenste Arten in unterschiedlichen Arbeitsumgebungen erfolgreich umgesetzt.
WIR: Können Sie da konkreter werden?
Fröleke: In einem Projekt haben wir beispielsweise die Materialversorgung untersucht. Es kam heraus, dass das Material vom Monteur selbst mit einem Handwagen abgeholt werden muss. Die Produktion steht während dieses Arbeitsschrittes also still. Der Mitarbeiter lädt stattdessen das Arbeitsmaterial auf den Wagen und zieht diesen zurück zu seinem Arbeitsplatz. Wir haben diesen Prozess so reorganisiert, dass der Monteur jetzt mit dem Material bedarfsgerecht beliefert wird und keine weiten Wege mehr zurücklegen muss. Anstatt Mann-zu- Ware funktioniert der Ablauf jetzt nach dem Ware- zum-Mann- Prinzip. Das haben wir durch die analytische Trennung der Arbeitsschritte Materialversorgung und Materialverarbeitung erreicht.
WIR: Wie sieht das dann in der praktischen Umsetzung aus?
Fröleke: Wir haben die Arbeitsumgebung nach ergonomischen und schlanken Kriterien und neu gestaltet. Ergonomisch konfigurierte Arbeitsstationen wurden in diesem Beispiel in einer I-Linie angeordnet. Sie verfügen z. B. über ein optimiertes, spiegel- und schattenfreies Beleuchtungskonzept und lassen sich elektrisch in der Höhe verstellen oder neigen, um nur zwei Möglichkeiten zu nennen. Dadurch lassen sie sich an verschiedenste physiologische Anforderungen anpassen. Das gewährleistet ein angenehmes Arbeiten. Der Monteur verarbeitet das Material an dieser Arbeitsstation nach dem First- in-first- out-Prinzip (Fifo) an den Werkstücken, welche eines nach dem anderen über eine Rollbahn an der Arbeitsstation ankommen. Um einen schlanken und reibungslosen Arbeitsprozess zu gewährleisten, gehen leere und gekennzeichnete Materialboxen ebenfalls über eine Rollbahn direkt an das Materiallager, wo sie automatisch eine Materialbestellung auslösen, die der dortige Mitarbeiter bearbeitet, die befüllten Boxen in einen Fifo-Wagen lädt und diesen zurück zur Arbeitsstation führt. Auf diese Art und Weise vermeiden wir einen Produktionsausfall infolge der Materialbeschaffung durch den Mitarbeiter selbst und sorgen für einen schlanken Materialfluss. Durch die analytische Trennung der Prozesse, also die eigentliche Prozessoptimierung, setzen wir aber auch eine spürbare Entlastung der Mitarbeiter um, die durch den ergonomisch ausgestatteten Arbeitsplatz noch verstärkt wird. Das führt zu einer erhöhten Mitarbeiterzufriedenheit, zu deutlich reduzierten Fehlzeiten und zu einem kontinuierlichen Output.
WIR: Können Sie das mit Zahlen belegen?
Fröleke: Rein auf die Produktion bezogen, ließen sich die Produktionskosten im beschriebenen Fall um 17 % reduzieren, wenn Lean Ergonomics richtig geplant werden. Nicht eingerechnet sind da die Einsparungen auf Grund des optimierten Lagermanagements, welche sozusagen als Komplementäreffekt durch Lean Ergonomics in dem eben beschrieben Beispiel eintreten. Volkswirtschaftlich gesehen ist der Schaden durch Produktionsausfall in Folge von Fehlzeiten beträchtlich. Die Bundesanstalt für Arbeitsschutz und Arbeitsmedizin (BAuA) spricht für das Jahr 2014 bundesweit von 90 Milliarden Euro, die an Bruttowertschöpfung verloren gehen, weil Beschäftigte u. a. an muskuloskelettalen und anderen Schäden erkranken und arbeitsunfähig sind. Die Ursache lässt sich im Großen und Ganzen auf nicht-ergonomische Arbeitsumgebungen zurückführen. Diese Zahlen verdeutlichen das Potential von Lean Ergonomics.
WIR: Herr Fröleke, vielen Dank für das Gespräch.